I've been playing with screen printing off and on over most of the summer. The biggest problem I've had (among all of the big problems I've had

I spread black fusing paint on the screen and then squeegeed it onto the glass. The paint was not thick enough and I got more of a blob than an image. Barry suggested I get some flux to add to the paints, so I got some of that. This is a white powder that you mix with the paint. It thickens it up and also lowers the maturing temp a bit, which was good since the paints mature between 1400 and 1450 and for testing I didn't really want to go to full fusing temps since I was using single layer glass. On this attempt I could tell it was a lot better when I squeegeed the paint. It didn't help my ability or the image, but the paint was much better.

Here is the 3rd attempt I did with the first image I was trying to use after it was fired:
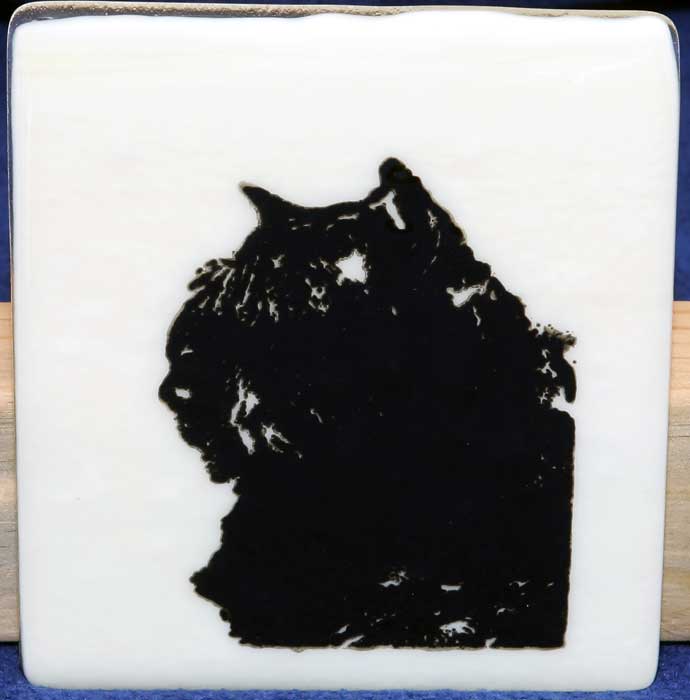
I didn't have the detail I was hoping for so next I went to a sold profile. I'll show a picture of that one in a bit.
A few weeks ago I read the post listed above about a place that prints decals for ceramics and glass which sounded pretty interesting and wasn't all that expensive.
What you do is create a page for your images that is 10"x15" and has what ever you want on it that you want decals made of. You can put as much as you can fit on the page and he prints it off and sends you the sheet. You then cut out the images to fuse on your glass. They do a print run once a week for normal priority and you have to have your order in by the day before. I had my sheet a couple of days after their print day.
I picked a handful of images to test it with and didn't fill the page as full as I could. I figure if they come out good, I'll be getting more later. I cut out and fused 3 of the images from my page and pretty much followed the directions on their web site other than I speeded up their schedule a bit and I did use Bullseye glass. They said that Bullseye may not be as smooth as the decals need to keep from getting bubbles with. I was careful to squeegee the decals on real well although I did still get a few small pin prick type bubbles that formed and popped. I didn't find them all that bad although I can see for something really important it may be better to go with Spectrum that has a smoother finish than Bullseye.
2 of the decals I put on solid colored glass and one of them I put on Crystal Clear Tekta. I can see where the image will need to be a certain type to work with clear as the image I used was washed out a bit. I can see the potential for something like a sun catcher with a very colorful image on it that would work well. The printer does not print white, so if you have white in your image you put it on white glass to add the white areas or keep that in mind so you can work around it. The flowers I did had some white in them so I put it on a white piece of glass.
Here are the images I did:
This one of my pictures of a yellow Lilly:

This is a picture of one of our Bouviers that I did on a clear piece of Tekta. I have a white piece of glass behind it so it's easier to see.

This image has two 5" circles. The red on the left is the decal and the yellow on the right is my screen print I mentioned above. The whitish areas around the head is a little bit of light reflecting and not the screen print itself.

And here is my decal sheet with the images cut out and the others still on it. You can see I had lots of room to put more stuff if I wanted to squeeze them in some.

The decals fused on the glass really well. They are fused in permanently and you can't feel them. One thing I did notice though is that the film that the image is printed on does show a little bit when you hold it just right in the light. The web site says this burns off but evidently it doesn't or this part doesn't burn off. I used a clunky pair of scissors to cut them out (I didn't feel like going upstairs and hunting up a small snipping pair that would have worked better) so I was about 1/4" or so away from the edges of the image itself. Next time I won't be so lazy and will get a pair that will let me snip right up to the image.
So there you have it. I can see some good possibilities with the decals and I think that it will be easier than trying to screen print some of the things I want to put on glass. As soon as I get time to go through some of my images and find those that I think will work good I'm going to order some more.
Mike