Unfortunately, I found out that it isn't just a simple matter of taking in a sheet of Bullseye glass, uploading an image and watch it cut out all of the things I couldn't cut out by hand. It requires files created in a CAD program and processed with the software of the waterjet machine that takes into consideration the path of the cuts, the thickness of the material, the shapes of the items being cut, speed of the cut, the length of time of the job, the width of the cutting stream and a number of other things... all which contribute to how much it's going to cost. The real road blocks that I found though were, one, finding a place that would cut thin glass (not all do or know how to do it even if they are willing to) and two, getting my images converted to a CAD program so I wouldn't have to pay to have it done by the waterjet shop, which can add a lot to the cost. One place had a quote of $30 a segment of the part being converted... if you already had it in a format that was ready to be converted.
I have done a lot of stuff in Photoshop and have for years (since back to version 6 and that isn't CS6 either

Well, I sorta gave up on the idea.

Maybe it's because there are now more places doing waterjet but this time I found more info. I even found that there was a guy in my town that had a waterjet shop AND a glass studio. He did a lot of art glass work for people as well as his own stuff. I sent him an email outlining my project and asking for a quote. I had heard he was pretty busy and he must have been because I didn't receive a reply back, so I kept looking for other places. Mostly I was looking for one that had on their web site that they did thin glass (if they mentioned art glass it was even better) and that small jobs were ok and ideally that they were on the West coast. If I was going to have to ship glass there and pay for shipping back, I wanted to keep it close if possible. A number of places seemed to be back East and in the Mid-West regions but I did find a few places in Seattle and California that seemed like good prospects. First though I had to get my images fixed up so that I could send them for a quote. So I got busy on that. I also wanted to be able to get the quote before the end of Bullseye Summer sale so I could buy the glass at half price if the cost of getting it cut didn't turn out to be over what I was willing to pay.
I tried converting my .png files again and even found an online web site that did conversions to .dxf and .dwg a number of formats... for free. I tried that and though the output was better than I was doing, it still wasn't clean outlines. So I kept looking. During my searches I ran across a neat outfit in Atlanta that does waterjet as well as laser and plasma cutting. The neat thing about them was that they had a program online that you could either draw your design or upload a .png image (or .dxf or .dwg), put in what size you wanted and pick from a number of materials, from plastic, to gasket, to leather, wood and metals of aluminum, stainless steel and cold and hot rolled steel and copper. They did other things to but they had these materials in stock in different thicknesses and grades. They did glass although they didn't seem to be too hot on it, so I didn't bother with that. But I did use them to check out my designs and tweak them. When you upload your image you can see a 3D image of what it will look like cut out from different angles. And you can pick one of their in stock materials and see what it would cost to have it waterjet cut. It was fun to play with and I did end up getting one of my designs cut out in T-304 Stainless Steel at 0.12 thickness. This is where I got to play with pricing. With something like this, it costs just about the same each for one item as it does each for a hundred of them. One item was 92.00 or I could get 5 of them for 92.00 or 10 for 92.00 or... well, you get the idea.

Anyway, back to my images. To be honest, I finally gave up trying to find a converter or a CAD program that was simple enough that even I could figure it out. So I started looking for drafting type services that would convert it for me as well as cleaning it up and making it so it would work with a waterjet machine. I only had 3 files to convert but one of the files had 5 parts. Some of the places would have cost me almost as much as the glass, so I went looking at off shore locations. I usually try to stay with US companies and though I know there must be some out there that are reasonable for what I needed, I just couldn't find any without sending a lot of emails asking for quotes since nobody gives an indication of price on their web pages. The place I finally found is in India and they do exactly what I needed done... at a total cost of 22.05 for all the files in just 24 hours.
Anyway, while my files were being converted I found another waterjet shop close by that was just north of Salem, Oregon, which is about 35 minutes South of me (depending on traffic on I5). I sent off an email to them and got a reply back the same day. After spending a couple of days going back and forth on what I wanted and the best way to do it, I was able to send my files down to him and got a quote for all of the stuff I wanted cut out of 2 full sheets of Bullseye Black, and one full sheet each of Red, Green and Yellow (I was going to use Cobalt Blue but decided it was darker than I wanted at this time). What cost the most with the cutting was the one group of 5 pieces, which are small and round and took a lot of cutting.
The person doing the waterjet cutting had them done within a few days after I dropped off the glass, which was faster than he had said it would take. When I arrived at his shop and got to see the results, I was extremely happy to see that they came out looking great. He said that he only broke one little piece, which was not a problem as I had extras of those cut. He had to put tabs on all of the pieces so that they would not bounce out of the glass after it was cut and he said he should have made a little bit bigger tabs as he had to slow down a bit because the cut pieces did want to bounce around a bit. Actually, I expected more breakage, so one little piece was very good in my book.
I am going to have to do a better job of communicating what I wanted next time though. I wasn't very clear on a couple of things and it ended up causing him to cut less of a one object and more of others, although it ended up leaving more glass left over than I expected, which will be put to good use later. I should have either taken one of my paws with me or included a picture of what I was looking for, which I will do next time I have some stuff cut out by waterjet. Besides that, the cutting was very impressive and I'm very happy with it.
Here are some pictures of what was done:
This shows the pieces after they were cut but before I fused them. This is the base blank for the paw and the pads that sit on top of it. One of the little pads is what broke:
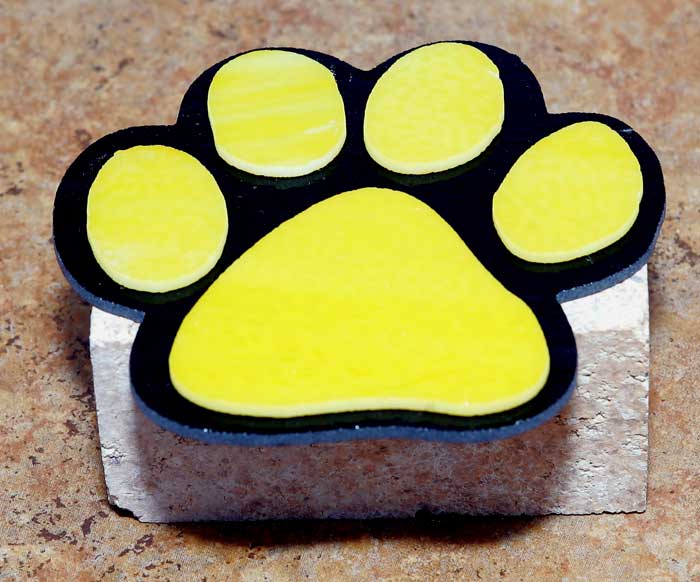
This is the profile I had done in 3 sizes (that is paper towel lint on them which only shows up in pictures.

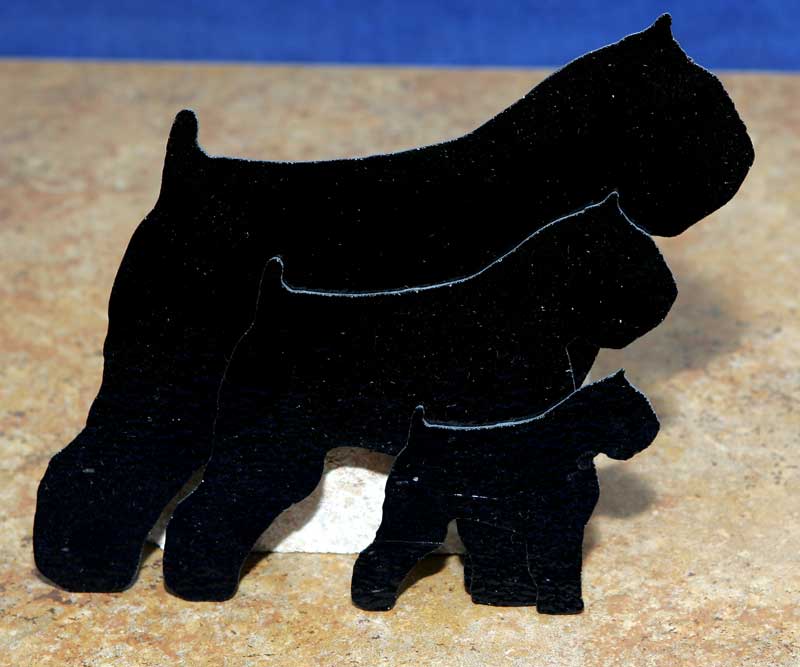
Here are three of the paws after they were fused but before slumping:
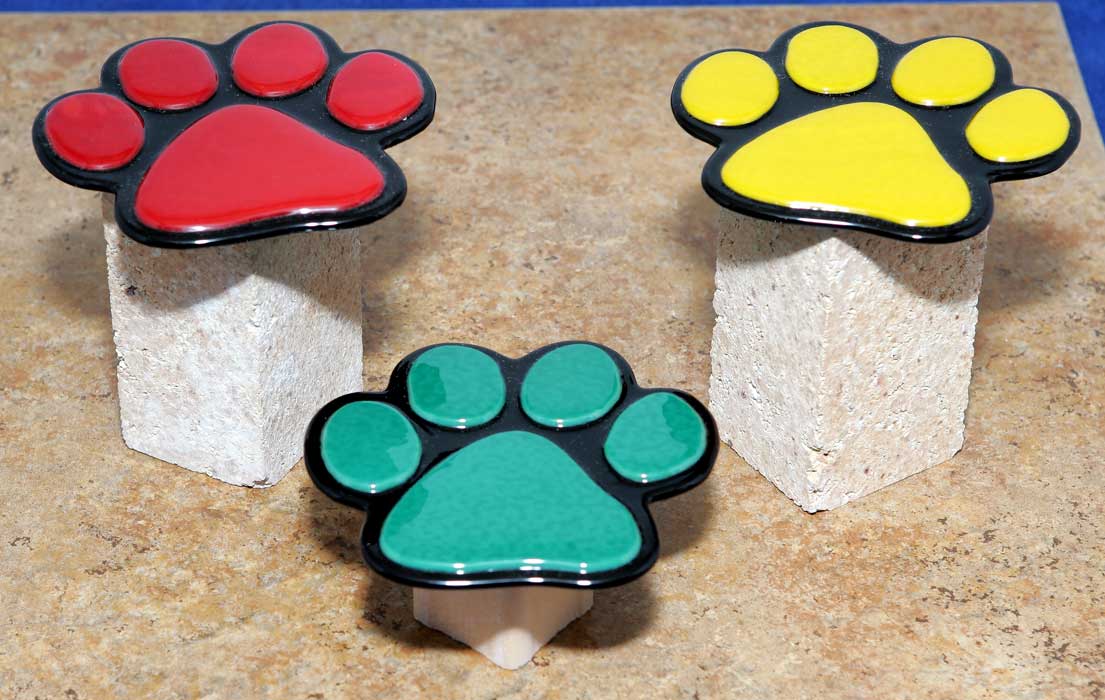
And here are three of them after they have been slumped:
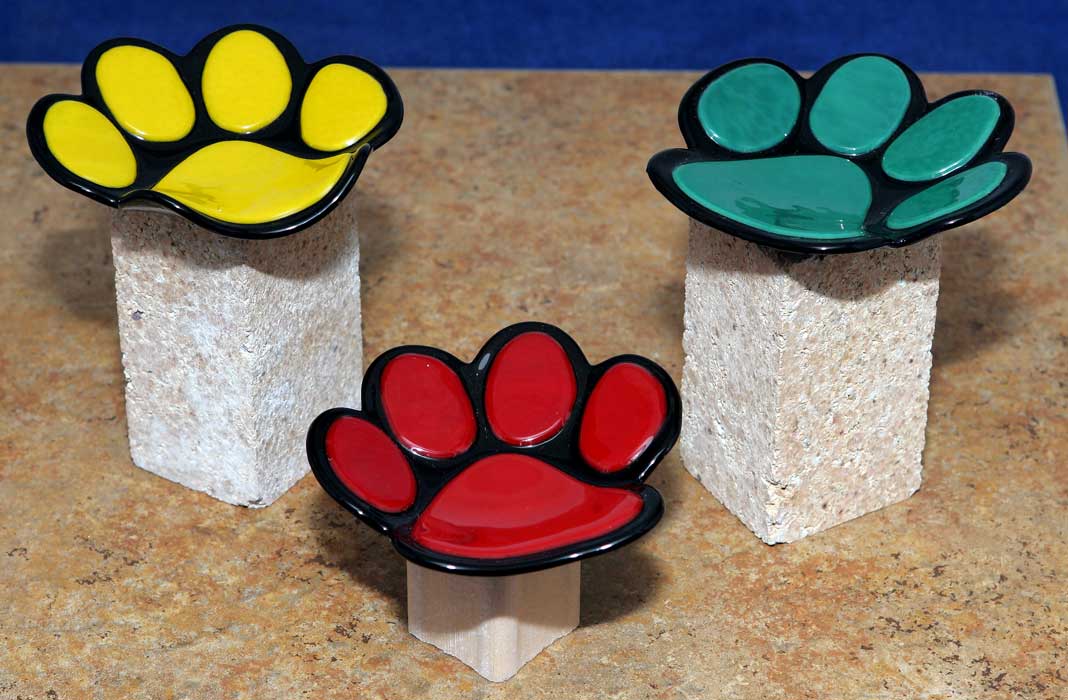
All in all, I was pretty happy with the outcome. Now that I understand the process a little better I hope to do it a bit cheaper next time and now that I know he can cut Bullseye glass without problems, I already have some more ideas of things I'd like to try.
Mike